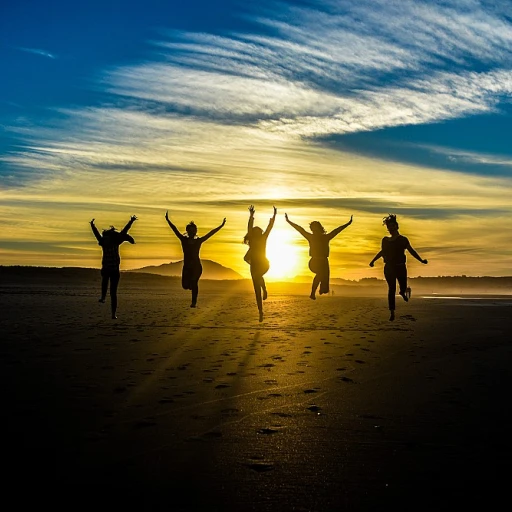
Understanding Metal Cutting Fluids
Role and Importance in Machining Processes
Metal cutting fluids, often referred to as cutting oils or coolants, are integral to the machining and metalworking industry. These fluids serve multiple roles, including acting as a cooling agent, lubricating the cutting interface, and assisting in the removal of chips from the workspace. In machining processes such as cutting, grinding, and tapping, the application of these fluids is critical to achieving precision and enhancing the overall efficiency of the operation.Composition and Variability
The composition of metal cutting fluids is diverse, ranging from water-based solutions to oil-based and synthetic products. These fluids are designed to cater to various metalworking needs, from heavy-duty tasks requiring robust lubricants to environmentally friendly options for safer applications. The choice between semi-synthetic and synthetic coolants depends on the specific requirements of the machining process and the machinery used.Enhancement in Precision and Productivity
Incorporating cutting fluids in machining processes leads to significant advancements in precision and productivity. The effective use of coolant products like Anchorlube and Tap Magic can reduce tool wear and maintain the surface finish of machined parts. By minimizing friction and reducing the heat generated during cutting and grinding operations, these fluids help preserve the integrity of both the tool and the metal. Moreover, advancements in fluid technology, such as water-based and synthetic coolants, have made it possible to optimize operations without compromising performance. These cutting fluids play a pivotal role in ensuring tool longevity and boosting overall workflow efficiency. As we explore these impact aspects, it's important to also consider the environmental implications and safety standards associated with the use of cutting oils and lubricants in machining. For more on enhancing precision in metalworking processes, delve into advanced lamination detection techniques for tubing assembly.Types of Metal Cutting Fluids
Diverse Categories of Metal Cutting Fluids
In the world of metalworking, the choice of cutting fluid plays a vital role in influencing the efficiency of machining operations. There are several types of cutting fluids available, each with distinct characteristics tailored to specific metal cutting needs. These products are designed to serve various functions such as lubrication, cooling, and chip removal, ensuring optimal tool performance and longevity.
Soluble Oils and Semi-Synthetic Fluids
Soluble oils are a predominant type of cutting oil, known for creating a stable emulsion when mixed with water. This makes them effective in cooling and lubricating cutting tools in metalworking processes. Semi-synthetic fluids, on the other hand, blend the properties of both soluble oils and synthetic products. These fluids offer enhanced coolant properties along with a cleaner operating environment, reducing the residue on machines and tools.
Synthetic and Microemulsion Products
Pure synthetic coolants are water-based and contain no petroleum or mineral oils, making them an environmentally friendly option in heavy duty machining tasks. These products are often preferred for their excellent heat dissipation properties and minimal environmental impact. Microemulsion fluids represent another advanced category, providing a fine balance by merging water’s cooling capacity with the lubrication properties of oil, optimizing both tool life and surface finish quality.
Specialized Fluids for Focused Applications
There are also more specialized options such as grinding oils and hydraulic fluids, which cater to precise machining operations like cutting and grinding, ensuring smooth lubrication and heat management. These specialized fluids are essential for applications that require extreme precision and specific performance characteristics.
For those looking to delve deeper into the practical application of these tools in a high-tech production environment, consider reviewing the essential checklist for broad insights.
Impact on Tool Longevity
Maximizing Tool Life Through Cutting Fluids
The strategic application of cutting fluids plays a pivotal role in enhancing the longevity of metalworking tools. When selecting between cutting, grinding, and hydraulic fluids, one must consider the direct impact on a tool's efficiency and lifespan. The balance between the correct lubricant and the machining process could mean the difference between prolonged operational capability and premature wear. Understanding the physics behind metal machining underscores the importance of effective coolant. The right combination of cutting fluid properties, including the lubrication provided by cutting oils and the cooling effect offered by water-based solutions, contributes significantly to tool preservation. For instance, synthetic coolants and metalworking lubricants like those from renowned brands or semi-synthetic variants tailored to specific machining environments offer substantial improvements in tool durability. Moreover, heavy-duty metal cutting operations demand formulations that minimize friction and heat, which are two primary culprits in tool degradation. By reducing these barriers, cutting fluids improve the precision of the cutting and grinding process, ensuring tools maintain their edge for longer periods. Another dimension in enhancing tool lifespan is employing products that cater to both technical performance and environmental considerations, such as environmentally friendly cutting oils. These solutions ensure tools are not only effective but also compliant with current safety data and regulatory standards. In conclusion, by carefully selecting the appropriate metal cutting fluid while acknowledging the ongoing cost factor illustrated in the price product comparisons, companies can not only extend the life of their tools but also enhance their overall productivity in machining operations. More insights can be found by exploring understanding people-centric pay structures, as connecting these dots in work environments ensures comprehensive efficiency.Efficiency and Performance Boost
Boosting Operational Efficiency and Performance
Industrial applications have long recognized the importance of cutting fluids, particularly in metalworking and machining processes. A well-selected fluid can provide significant efficiency benefits, enhancing the performance of machines and tools. Let's discuss how cutting oils, water-based lubricants, and synthetic coolants can lead to a remarkable boost in operational efficiency. Cutting and grinding operations depend heavily on the suitable application of cutting fluids. Here are several key benefits:- Heat Dissipation: Fluids such as semi-synthetic and synthetic coolants play a crucial role in dissipating heat generated during machining. By reducing thermal stress on the cutting tool and the workpiece, they prevent damage and extend tool longevity. This contributes to fewer interruptions and more consistent processing quality.
- Lubrication: Effective lubrication minimizes friction between the cutting tool and the metal surface, reducing tool wear and maintaining high-quality surface finishes. Whether using cutting oils or water-based solutions, the correct fluid choice can significantly improve tool life and overall efficiency.
- Chip Removal and Flush: Proper cutting fluids assist in clearing chips from the cutting area, preventing them from causing any damage to the tool or workpiece. Anchorlube and similar products are specially engineered to offer superior performance in chip evacuation, therefore maintaining smooth operations.
- Productivity Enhancements: With the use of environmentally friendly, advanced metal cutting fluids, the need for tool changes is reduced. This leads to extended machine uptime and improved productivity.
Environmental and Safety Considerations
Balancing Environmental Impact and Workplace Safety
In the realm of metalworking, the focus on sustainability and safety is becoming increasingly crucial. As industries lean towards eco-friendly practices, cutting fluids are not left out. These essential lubricants have seen innovations aimed at minimizing their environmental footprint while enhancing safety for operators.
Traditionally, cutting oils were primarily mineral-based, leading to environmental concerns due to their disposal challenges and potential hazards. However, the shift toward water-based solutions has significantly reduced these risks. These alternatives offer similar efficiency in reducing friction between the tool and metal, ensuring prolonged tool lifespan as discussed in earlier sections, while being easier to treat and dispose of.
The introduction of synthetic and semi-synthetic coolants has been a game-changer. These products often combine the lubrication properties of oils with the enhanced cooling capacity of water, offering superior performance in metal cutting applications. Also, they tend to biodegrade more swiftly, which mitigates their impact on the environment.
Another important aspect of modern cutting fluids is their formulation to minimize health risks associated with prolonged exposure. Ensuring a product aligns with safety data sheets and regulatory standards is crucial for workplace safety. This commitment to safety extends to the adoption of more environmentally friendly lubricants, such as the ones offered by recognized brands like Anchorlube and Tap Magic, which are formulated to minimize harmful fumes and skin irritations.
Finally, it's pertinent that industries consider the entire lifecycle of the cutting fluids they use, from application to disposal. Opting for recyclable and reconditioned fluids can further reduce environmental burden. As we look towards the future, innovations will likely continue to focus on developing cutting fluids that not only boost machining performance but also uphold high standards of safety and sustainability.