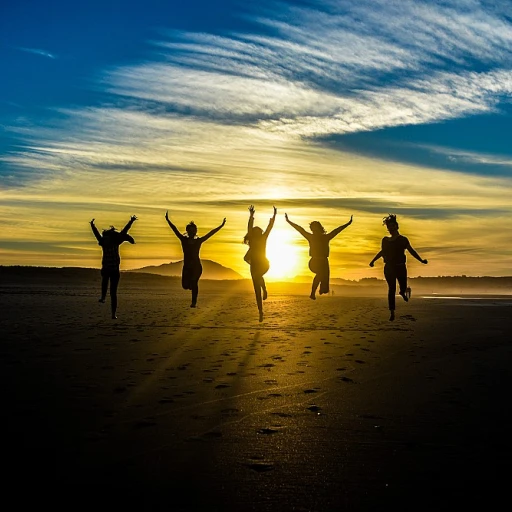
The Basics of Oxy-Fuel Cutting
The Science Behind Oxy-Fuel Cutting
Oxy-fuel cutting, often referred to as oxy-acetylene cutting, is a proven technique in the metalworking industry. This process involves using a cutting torch to heat the base metal to its ignition point. The torch utilizes oxygen and a fuel gas—most commonly acetylene—to create a high-temperature flame capable of severing through steel and other metals.
The principle of this method revolves around the combustion of the fuel gas with the cutting oxygen to produce the intense heat necessary to melt and cut the material. When the torch is applied to the steel, the combination of high-pressure oxygen and acetylene creates a temperature capable of exceeding the melting point of the metal.
One of the critical factors in effectively using an oxy-fuel cutting system is understanding the concept of pressures. It is important to monitor pressures since they dictate the flame characteristics and subsequently affect the precision of the cut. Mismanagement of these pressures can lead to ineffective cutting or potential safety hazards, which we will explore further.
Oxy-fuel cutting requires meticulous attention to the size of the cutting torch and the specific psi settings for both the oxygen and acetylene. Pressure settings influence the efficiency and quality of the cut significantly. Skilled operators understand the importance of adjusting gas pressures to suit the metal thickness and specific location of the cut. Correct psi settings ensure a clean and efficient cut, helping operators to master this technique effectively.
The role of meter banks in managing gas flow and optimizing pressure settings is an advanced element of modern oxy-fuel cutting practice. These sophisticated mechanisms allow for precise control and are integral to achieving optimal results in this evolving field.
Why Pressure Matters
The Role of Pressure in Efficient Cutting
Understanding the right pressure settings in oxy-fuel cutting is crucial. Gas pressure, particularly from oxygen and acetylene, directly influences the efficiency and precision of the cut. When using an oxy-fuel cutting torch, the cutting oxygen must be regulated to maintain the right pressures for optimal performance, especially when dealing with varying metal thickness. The cutting process relies heavily on the melting point of the base metal, and here the role of the preheat flame becomes significant. A well-regulated pressure ensures the flame provides sufficient preheat and cuts through the steel effectively. An imbalance in the gas pressure can lead to inefficient heat distribution, potentially compromising the cutting quality. Pressure issues can cause the torch to produce uneven cuts, excessive dross, and potentially dangerous situations. This might occur if the oxygen or acetylene pressures oxy are not within the recommended settings. It's essential to maintain the equipment for accurate psi readings – over/under calibrated gauges can mislead operators, risking poor quality cuts or equipment damage. Achieving the right balance in oxy acetylene pressures is paramount as it directly impacts the quality and speed of the manual cutting process. Operators should familiarize themselves with optimal psi settings for different material sizes, practicing adequate skills to master the cutting technique and maintain constant performance. For more insights on mastering such technical skills, consider exploring the role and intricacies of equipment maintenance in hydraulic systems.Optimal Pressure Settings
Achieving the Right Balance in Pressure Settings
When diving deeper into the process of oxy-fuel cutting, it becomes evident that pressure plays a pivotal role in achieving effective cuts. The pressure of gases like oxygen and acetylene is central to the entire operation, and getting these settings right is essential for a clean and efficient cut. To begin with, the psi levels for both the cutting oxygen and the fuel gas must be controlled precisely. Typically, the oxygen pressure is significantly higher than the acetylene pressure, often in the range of 20 to 60 psi, depending on the metal thickness and the specific application. Acetylene pressure, on the other hand, typically hovers around 5 to 10 psi. These settings are not arbitrary but are carefully calculated to ensure the optimum combination of heat and flame characteristics required to cut through materials like steel. The size of the cutting torch tip and the specific type of metal being worked on, such as steel or another base metal, will dictate the exact pressure settings. It is crucial to adjust based on the task at hand, as different materials and thicknesses will react differently to specific pressure levels. Moreover, mastering the regulation of these pressures is an art in itself. Consistency is key, as fluctuations can lead to poor quality cuts or even hazardous situations. Just as one must master cutting techniques, understanding pressure regulation can greatly enhance both the quality and speed of oxy-fuel cutting operations. Understanding and optimizing gas pressure settings in fuel cutting operations can streamline your workflow, much like how efficient payroll solutions can streamline administrative processes in your organization. Proper management and adjustment of pressure settings not only improve cutting outcomes but also enhance safety and efficiency.Common Mistakes and Solutions
Missteps and Effective Remedies in Oxy-Fuel Cutting
Achieving the perfect cut with oxy-fuel systems can be challenging. Missteps often occur with incorrect psi settings, leading to suboptimal results or even equipment damage. Understanding how to mitigate these common mistakes enhances cutting efficiency and safety. One frequent issue is misjudging the oxygen pressure. Too low, and the torch does not generate enough heat to efficiently melt the base metal, while too high can oxidize the metal rather than cut it. Technical guidelines specify the appropriate psi oxygen setting according to the metal thickness and type. Similarly, acetylene or any other fuel gas pressure must be correctly aligned with the task. For instance, when working with thicker steel, the psi acetylene needs adjustment to supply sufficient fuel heat without excessive flame. Oxy acetylene cutting requires careful consideration of the gas supply to maintain a stable flame. Uneven pressures oxy between the oxygen and fuel gas can distort the flame, producing inefficient cuts. Regularly checking the gas pressure assists in avoiding these inconsistencies. Another error involves incorrectly positioning the cutting torch. The torch size and angle are critical for a clean and precise cut. For effective results, maintain a proper distance from the workpiece—doing so prevents accidental melting of areas beyond the intended cut. Beyond technical adjustments, mastering torch control is crucial. Unsteady manual handling creates uneven cuts and a poor finish. Practicing consistent movements around the cutting location can boost precision and confidence. Lastly, safety gear is often overlooked. Adhering to safety considerations ensures protection from potential hazards posed by cutting flames, sparks, and flying metal debris. These common mistakes underline the need for diligence and care in oxygen acetylene processes. By understanding and avoiding these errors, you can truly master the art of oxy-fuel cutting.Safety Considerations
Ensuring Safety in Oxy-Fuel Cutting Operations
Working with oxy-fuel cutting technology requires vigilance and a robust understanding of safety protocols. While the other sections touch on the intricacies of pressure settings and optimizing performance, it's crucial not to overlook the safety aspects inherent in dealing with high heat and flammable gases like oxygen and acetylene. When using a cutting torch, the right balance of oxygen and fuel gas is essential to maintain a steady flame and prevent dangerous situations. Uneven or incorrect gas pressures can lead to backfires or flashbacks, posing risks to operators and the surrounding environment. Here are some key safety considerations:- Equipment Checks: Regularly inspect hoses, regulators, and the cutting torch itself for any signs of wear or damage. Never use damaged equipment as it can lead to gas leaks or uncontrolled flames.
- Pressure Control: Always verify that gas pressures, specifically the psi for oxygen and acetylene, align with manufacturer guidelines for the size and type of cutting process being performed.
- Fire Prevention: Keep a fire extinguisher and other fire suppression tools within reach. A clear workspace free of flammable materials is mandatory to reduce fire risks.
- Safety Gear: Wear protective gear such as gloves and goggles to shield against sparks, heat, and ultraviolet radiation.
- Ventilation: Ensure adequate airflow in the cutting location to prevent the accumulation of combustible gases, which can lead to dangerous explosions.
- Competency Training: Operators should be trained in oxy-fuel processes, ensuring they master the correct procedures and understand how to respond to emergencies.
Future Trends in Oxy-Fuel Cutting Technology
Advancements in Oxy-Fuel Cutting
The future of oxy-fuel cutting technology stands on the brink of significant advancements. As the industry continues to evolve, several key trends are emerging, poised to reshape how metal cutting is approached.- Automation Integration: Automation is increasingly being integrated into oxy-fuel cutting systems, allowing for more precise control over pressures and flame settings. This trend will likely minimize human error and ensure optimal cuts irrespective of the location.
- Innovative Gas Mixes: New fuel gas combinations and enhancements to oxy acetylene mixtures can improve flame characteristics, impacting gas pressure requirements and offering more efficient fuel consumption.
- Enhanced Safety Features: Modern cutting torches are being designed with improved safety mechanisms to protect operators from potential hazards associated with high psi pressures. As mentioned earlier, safety remains a critical aspect, and innovations in this arena are prominent.
- Materials Science Breakthroughs: Advancements in metal alloys and a better understanding of metal thickness and melting points can inform new approaches to oxy fuel systems, allowing for specialized applications tailored to specific cutting needs.
- Smart Welding Technologies: Integration with smart technologies will facilitate improved monitoring and control over welding cutting processes. Real-time data on cutting oxygen, base metal temperatures, and heat distribution can optimize performance and longevity of equipment.
- Sustainability Efforts: With a growing emphasis on sustainability in manufacturing, the focus is shifting towards reducing emissions from acetylene welding and fuel cutting processes, promoting greener methods.