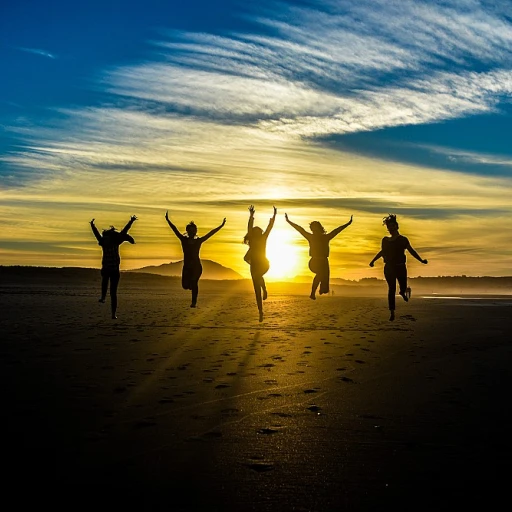
Understanding the Importance of PPE in Welding
The Critical Role of Personal Protective Equipment in Welding
Welding is a high-risk task that involves extreme conditions and requires proper protection to ensure the safety of those undertaking it. The nature of welding work exposes welders to numerous hazards such as intense heat, sparks, arc radiation, and the risk of fire. Hence, investing in the right personal protective equipment (PPE) is not an option but a necessity for welding safety.
Proper welding attire serves as a barrier between the welder and these potential threats. Protective clothing, such as flame-resistant jackets and trousers, and accessories like welding gloves, are essential to defend against burns and thermal injuries. Additionally, the significance of wearing a welding helmet, particularly those with auto-darkening features, cannot be overstated. These helmets protect against bright light and arc radiation while facilitating visibility during arc welding.
While head and body protection are paramount, equally crucial is respiratory protection. Fumes and gases emitted during the welding process can be hazardous when inhaled. Therefore, incorporating appropriate safety glasses and respiratory gear into the PPE regimen helps mitigates the inhalation risks linked to arc welding.
The plethora of available protective equipment varies, and welders have a wide array of options with features to cater to different needs. For example, some brands promise "free shipping" and other benefits to incentivize purchases.
Despite these offerings, implementing appropriate PPE with all its components remains a challenge due to cost and awareness factors. Moreover, ensuring compliance with regulatory standards is pivotal for workplace safety and often requires rigorous attention.
To remain updated on the constantly evolving landscape of protective equipment and its regulations, welders can benefit from continuous learning and stay informed about current trends in safety equipment by referring to resources such as the mastering data privacy.
Key Components of Welding PPE
Essential Components for Ensuring Welding Safety
In any welding environment, Personal Protective Equipment (PPE) is indispensable for safeguarding welders from the inherent risks and hazards. Understanding and utilizing key components of welding PPE is critical in minimizing exposure to heat, sparks, and harmful radiation, ensuring enhanced safety.- Welding Helmets: The most recognizable piece of safety gear, the welding helmet, serves as the first line of defense against arc flashes and sparks. Advanced designs now include auto-darkening filters, allowing welders to maintain their focus without manually adjusting their protective lenses.
- Welding Gloves: These protective gloves provide vital insulation against the intense heat and arc burns characteristic of welding processes. Made from heat-resistant materials, welding gloves act as a barrier to prevent skin exposure to sparks and spatter, effectively reducing the risk of injury.
- Fire and Flame Resistant Clothing: Informing about clothing designed to tolerate extreme temperatures while preventing ignition is essential. This includes jackets and aprons made from flame-resistant fabrics, ensuring that welders are protected from potential fires sparked by stray arc strikes.
- Safety Glasses: In addition to helmets, safety glasses offer an extra layer of protection against flying debris and radiant energy, which can still pose threats despite wearing full helmets.
- Respiratory Protection: With the hazardous fumes produced during welding, wearing suitable respiratory gear is a must. This protective equipment ensures that welders are not inhaling dangerous substances, safeguarding their respiratory health in the long term.
Innovations in Welding PPE Technology
Revolutionary Developments in PPE for Welding Safety
Welding, a vigorous and dynamic process, demands the highest standards of safety. Over the years, innovations in protective equipment have transformed how welders protect themselves from the inherent risks, such as sparks, heat, and radiation. One of the most significant advancements in recent times is the development of auto-darkening welding helmets. These helmets have sensors that detect the welding arc, automatically adjusting the lens to protect welders from intense light and radiation. This technology allows for seamless transition between tasks, minimizing the need to constantly lift or reposition the helmet, enhancing productivity and safety. Another area of focus is the improvement of welding gloves. Modern versions incorporate high-quality materials designed to provide superior heat and flame resistance. They are crafted to offer better dexterity, giving welders the ability to safely handle tools and equipment without sacrificing protection. Safety glasses have also seen a major upgrade. Today’s versions offer improved clarity and are treated with anti-scratch and anti-fog coatings, ensuring optimal visibility even in challenging conditions. Respiratory protection has moved forward with advancements in filtration systems, helping to effectively guard against fumes and particulates often generated during welding operations. Clothing options for welders have expanded as well, with the introduction of fire and flame-resistant fabrics that not only protect against heat and sparks but are also lightweight and breathable, improving comfort for longer wear times. These innovations highlight the industry's continuous evolution towards better safety standards and https://www.work-tech-institute.com/blog/exploring-the-intricacies-of-screw-machining provides insights into how advanced technical processes contribute to these enhancements in personal protective equipment (PPE). With free shipping options increasingly available, access to top-notch welding PPE is more convenient than ever, ensuring that welders everywhere can uphold stringent safety measures.Regulatory Standards and Compliance
Adhering to Essential Safety Norms
When it comes to welding, adhering to regulatory standards is vital for ensuring the safety and protection of welders. Personal protective equipment (PPE) serves as a fundamental line of defense against the risks associated with welding processes, including exposure to intense heat, sparks, spatter, arc radiation, and potential fire hazards. Agencies responsible for occupational safety, such as OSHA in the United States, have established stringent guidelines to dictate the use of protective clothing, welding helmets, gloves, and other safety equipment.
Key components of welding PPE, such as flame and heat-resistant clothing, welding helmets equipped with auto-darkening lenses, and safety glasses, are all designed to mitigate risks. Compliance with these standards is often mandatory, influencing not only the choice of equipment but also its maintenance and regular inspection. Ensuring the proper fit and quality of PPE is crucial in protecting welders from occupational dangers and maintaining a safe working environment.
In addition to national standards, various international regulations influence the design and use of PPE across global markets. Such regulations advocate for the highest levels of safety and innovation in protective gear, urging manufacturers and employers to prioritize the well-being of welders throughout the welding process. By understanding and implementing regulatory requirements, the industry can maintain a high standard of safety and avert significant health risks.
Challenges in Implementing PPE in Welding
Addressing Barriers to Implementing Safety Gear
In the welding industry, the importance of protective clothing and gear such as welding helmets, gloves, and safety glasses cannot be overstated. However, there are significant challenges when it comes to implementing these essential protective measures effectively. Firstly, cost is a primary hurdle. High-quality PPE, which includes flame-resistant clothing, auto-darkening welding helmets, and specialized gloves, often comes with a steep price tag. While these items are crucial for protection against heat, sparks, and arc welding hazards, many smaller operations struggle with budget constraints. The availability of options like free shipping can slightly alleviate costs but doesn't solve the overall financial burden on smaller businesses. Another challenge is the issue of compliance and adherence to regulatory standards. Safety equipment must meet specific criteria to ensure adequate protection, but not all employers prioritize this due to either lack of awareness or reluctance to invest in superior safety gear. Education and training play a vital role in addressing these gaps, ensuring that all stakeholders understand the long-term advantages of investing in compliant PPE and the risks associated with non-compliance. Furthermore, comfort and practicality are often overlooked factors that impede the widespread adoption of PPE. Welders frequently report discomfort or reduced mobility when wearing protective equipment during welding processes, leading to inconsistent usage. Innovations in materials used for helmets and clothing have improved comfort, but ongoing advancements are necessary to enhance wearability without compromising safety. Lastly, changing workplace cultures can also be a barrier. Establishing a safety-first mindset requires a shift in perceptions at all organizational levels. Employers must actively promote the use of PPE and foster an environment where safety is a shared responsibility among welders and management alike. Each of these challenges requires concerted efforts from manufacturers, regulatory bodies, and employers to ensure that welding safety equipment is both accessible and acceptable, minimizing the risks associated with welding activities.Future Trends in Welding Safety Equipment
Looking Ahead: The Evolution of Safety Equipment
The welding industry continues to evolve, driven by technological advancements and a growing focus on safety. The future of welding safety equipment promises to bring even more sophisticated solutions targeting effective protection against various hazards. Today’s protective equipment, including helmets, gloves, and clothing, is advancing with innovative designs improving ergonomics and ease of use.
Auto-darkening welding helmets, for instance, are continuously being refined to provide better protection against arc and sparks while becoming more adaptable to different welding processes. These helmets can automatically adjust the tint level, allowing welders to maintain visibility and protect their eyes without needing to lift the visor. This development significantly reduces the risk of exposure to harmful radiation and sparks.
Moreover, innovations in materials for protective clothing and gloves are coming to the fore. New flame-resistant and heat-resistant fabrics are being designed to offer superior protection while enhancing comfort and mobility. Wearable technologies in PPE are also beginning to emerge, integrating sensors to monitor a welder's exposure to risks such as high temperatures or radiation, which could help prevent accidents before they happen.
As the implementation of these innovations continues, alignment with regulatory standards and compliance will remain crucial. New standards may be introduced to incorporate these advancements, ensuring worker safety remains a priority.
Overall, the emphasis on improving welding safety will drive further enhancements in PPE designs and functionality, equipping welders with advanced tools to protect themselves effectively in diverse working conditions.