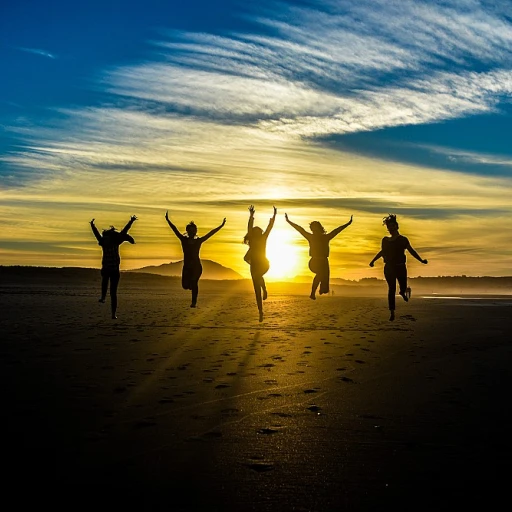
Understanding the Role of Lubricants in Metal Machining
The Significance of Metalworking Fluids
Metalworking fluids, often referred to as lubricants, play a pivotal role in machining operations. These fluids are crucial in optimizing the performance and longevity of cutting tools while ensuring superior surface finish and reduced tool wear. In the context of metalworking, whether you are dealing with high-speed CNC machining or conventional steel and cast iron applications, the choice of the right lubricant affects the overall efficiency of the process. In machining, a cutting tool generates a significant amount of heat due to friction. This is where metalworking lubricants come into play. By providing essential cooling and lubrication, they help in dissipating the heat generated and reducing the friction between the cutting tool and the workpiece. For example, cutting oil is often used when machining aluminum and titanium alloys to maintain the tool's performance and the machined part's integrity. Moreover, the use of cutting fluids, such as water-soluble and synthetic fluids, is vital in preventing the wear and tear of tools, thus extending tool life. These fluids also help in flushing away metal chips and debris, ensuring the machining area remains clean and functional during operations. Understanding the role of metalworking fluids is key to achieving optimal performance in any machining task, from milling stainless steel to tapping an intricate CNC design. For a deeper dive into related technologies, explore the role of screw machines in modern manufacturing, which also benefit significantly from effective lubrication strategies.Types of Lubricants Used in Metal Machining
Diverse Lubricant Options for Metal Machining
In metal machining, the choice of lubricant plays a pivotal role in optimizing performance. These lubricants, also commonly referred to as metalworking fluids, are essential in reducing friction and tool wear, enhancing the surface finish, and cooling the high-speed tools and the metal surface. Here’s a breakdown of the primary types of lubricants used in this industry:
- Straight Oils: These are non-emulsifiable oils often used in severe machining operations. They offer excellent lubrication properties but are not commonly used for cooling, making them less suitable for operations that require high cooling performance.
- Soluble Oils: Combining oil with water, soluble oils provide a balance between cooling and lubrication. These water-soluble cutting fluids can efficiently manage the heat generated during processes like CNC machining, improving tool life, especially when working with stainless steel and titanium alloys.
- Semi-Synthetic Fluids: These fluids offer a blend of soluble oils and synthetic components. They provide superior lubrication compared to soluble oils and offer enhanced cooling, making them a versatile choice for various machining operations.
- Synthetic Fluids: Made entirely without mineral oils, synthetic fluids excel in cooling and offer cleaning properties, which makes them ideal for high-speed applications. They are enhanced with additives to reduce tool wear and improve efficiency when cutting metals like aluminum and cast iron.
- High-Performance Additives: Additives play a critical role across the board, enhancing the performance of metalworking fluids. These include corrosion inhibitors for protecting machine surfaces and cutting tool edges, and extreme pressure additives to prevent the welding of metal surfaces during machining.
Each type of lubricant comes with its own advantages and potential drawbacks, which must be evaluated in conjunction with the specific requirements of the machining operation. For those looking to deepen their expertise in selecting the suitable metalworking fluid, explore more about the role of a certified manufacturing engineer who often oversees these critical decisions.
Factors Influencing Lubricant Selection
Key Considerations for Lubricant Selection in Metalworking
The process of selecting the right lubricant for metal machining involves multiple factors, as the choice of fluid can significantly impact the efficiency and quality of machining operations. Understanding these factors is crucial for ensuring optimal tool performance and longevity. One of the primary factors to consider is the type of metal being machined. For instance, machining operations involving aluminum or titanium alloys may benefit from different lubricants compared to those used for stainless steel or cast iron. The choice between cutting oils and water-soluble fluids often hinges on the specific requirements of the material. The machining processes themselves play a significant role in lubricant selection. High-speed operations, such as those conducted in CNC machining, demand lubricants that provide excellent cooling and reduce tool wear, thereby extending tool life. For operations involving high-speed steel cutting tools, a cutting oil with good thermal conductivity and stability is advantageous. Considering the type of cutting tool is also essential. Different cutting tools respond differently to lubricants. For example, tools used in threading operations may require a cutting fluid with specific additives to enhance surface finish and minimize friction. Additionally, the environmental and safety aspects should not be overlooked. Operators must balance performance efficiency with the safety standards of the working environment. Opting for a cutting fluid that complies with safety regulations helps in preventing accidents and ensuring a safer workplace. For more insights into enhancing safety in related operations, readers can explore essential safety gear. Lastly, the economic aspect cannot be neglected. The cost of lubricants, including the long-term financial implications of using a particular type of fluid, should be weighed against its performance benefits. This ensures efficient resource utilization in metalworking operations.Advantages and Disadvantages of Different Lubricants
Pros and Cons of Various Lubricants in Metal Machining
Choosing the right lubricant for metal machining involves weighing the advantages and disadvantages of each type. Each lubricant, from cutting oils to synthetic fluids, brings its own strengths and weaknesses to machining operations. Understanding these aspects can heavily influence tool life, surface finish, and overall machining efficiency.
Cutting Oils: Straight oils, known for their excellent lubricating properties, provide superior film strength, reducing tool wear significantly. They are widely used in operations involving heavy machining of materials like steel and stainless steel. However, their effectiveness in cooling is limited, as they do not conduct heat away from the tool as efficiently as water-soluble fluids. Additionally, cutting oils can lead to environmental concerns and disposal challenges, making them less appealing for eco-conscious operations.
Water-Soluble Fluids: These fluids combine water with oil or synthetic substances for better cooling capabilities. They are effective in reducing the high heat generated during high-speed machining operations. The water content ensures efficient coolant properties, making them popular for operations on titanium alloys and aluminum. Nonetheless, they can cause corrosion if the concentration is not properly maintained, and their need for regular maintenance can be seen as a disadvantage.
Synthetic Fluids: Developed to offer high performance without the environmental drawbacks of oil-based fluids, synthetic fluids are gaining traction in the metalworking industry. They provide excellent cooling and lubrication while minimizing residue. However, one should consider their compatibility with the metal being machined, as certain synthetic formulations may react with materials like cast iron or contribute to foaming issues.
Hybrid Lubricants: Blending the properties of oils and water-based fluids, hybrid lubricants are designed to harness the benefits of both. They typically offer a balance between cooling efficiency and lubrication capabilities. While they promise improvements in machining speed and tool life, the potential for complexity in formulation must be taken into account, especially when dealing with complex materials such as high-speed tool steel.
The decision to select a particular type of lubricant will hinge on factors like material type, machining processes, equipment, and environmental considerations. Each lubricant's unique balance of cooling and lubrication properties must be meticulously analyzed to optimize machining outcomes.
Innovations in Lubricant Technology
Innovations in Metalworking Fluids
In recent years, advancements in lubricant technology have significantly transformed metal machining operations. These innovations have not only improved the effectiveness of metalworking fluids but also enhanced machining performance by extending tool life and improving surface finish.
One notable development is the introduction of synthetic fluids, which offer an excellent balance between cutting efficiency and cooling properties. Unlike traditional cutting oils, synthetic fluids contain fewer impurities, providing a cleaner working environment and minimizing the risk of residue on machine parts. This is particularly beneficial when machining high precision components such as those made from titanium alloys and stainless steel.
In addition to synthetic options, water soluble oils have gained traction for their ability to effectively cool and lubricate during high speed machining. These fluids are designed to efficiently dissipate heat and reduce tool wear, making them ideal for CNC machining applications. Moreover, they are often tailored with additives that enhance their performance across various metals including steel, aluminum, and cast iron.
Additives play a crucial role in modern cutting fluids, providing specific benefits tailored to different machining needs. For instance, anti-wear additives can extend the service life of cutting tools by reducing friction, while corrosion inhibitors protect both the tool and the workpiece from rust and other forms of deterioration.
As environmental concerns continue to rise, biodegradable fluids have been developed, offering sustainable alternatives without compromising efficiency. These cutting fluids are formulated to break down more easily after use, minimizing environmental impact and promoting workplace safety.
These innovations in lubricant technology underscore the importance of selecting the appropriate metalworking fluid in accordance with the specific requirements of each machining operation. By doing so, manufacturers can optimize the performance, longevity, and safety of their metal machining processes.
Best Practices for Lubricant Application in Metal Machining
Ensuring Optimal Lubricant Application in Metalworking
In metal machining, applying the correct lubricant is as critical as selecting the right one. Ensuring the lubricant is used effectively can enhance cutting tool life, improve machine efficiency, and maintain a superior surface finish.- Consistent Monitoring: Regularly inspect the level and condition of the cutting fluids, oils, or coolants. Monitoring not only ensures that the fluid is clean and at the right concentration but also prevents problems such as tool wear or reduced tool life commonly faced in high-speed machining operations.
- Appropriate Lubricant Flow: Adjust the flow of lubricants such as cutting oil or metalworking fluids to guarantee a stable and sufficient supply during operations. An adequate flow helps in cooling, lubricating, and cleaning the cutting area, essential for machining materials like steel, aluminum, or titanium alloys.
- Proper Maintenance of Equipment: Ensure that all machining equipment, particularly those involved in CNC machining, are maintained to prevent any blockages or leaks in the lubricant delivery system. Efficient delivery systems are vital for the even distribution of synthetic fluids or straight oils over the cutting zone.
- Employ the Right Additives: Using the correct additives in synthetic fluids or water soluble oils can enhance the lubricant's performance. Additives can offer extra benefits, including better cooling properties, extended tool life, and enhanced final surface finish on metals such as stainless steel or cast iron.
- Training and Safety: Provide adequate training to operators regarding the handling and application of metalworking fluids. Safety considerations are necessary since improper use can lead to detrimental outcomes for both machining operations and worker safety.