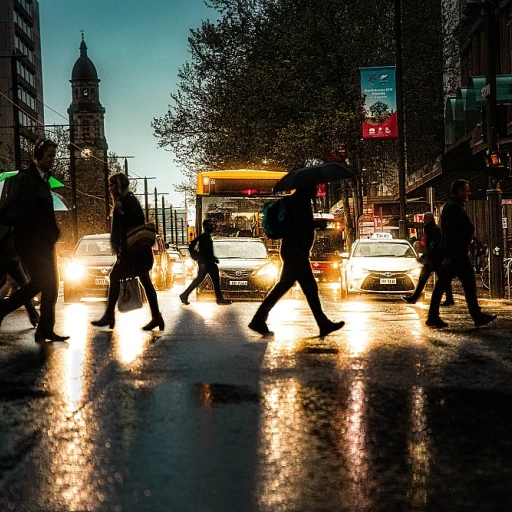
Understanding Metal Cutting Coolant
The Basics of Metal Cutting Coolant
Metalworking operations such as cutting, grinding, and sawing rely heavily on the right fluids to maximize efficiency and tool life. The use of cutting fluids is central to these processes. They serve not only as lubricants but also as vital components that enhance machine performance and extend the life of both tools and machinery. In the realm of metalworking, the term "coolant" is often used interchangeably with cutting oils and metalworking fluids. These products come in a variety of formulations, such as soluble oils, semi-synthetic, synthetic, and heavy-duty options. Each type is designed to address specific challenges and requirements dictated by the nature of the workpiece, the cutting conditions, and the type of tool or machine being used.Attributes of Effective Cutting Fluids
- Lubrication: A key function of cutting fluids is to minimize friction by providing a lubricating layer between the tool and the workpiece. This can greatly influence the cutting tool's longevity, particularly when working with hard metals or high-speed cutting operations.
- Cooling: Metal cutting operations generate significant heat, which can negatively impact both the workpiece and the cutting tool. The use of coolant helps dissipate this heat, reducing thermal deformation and enhancing the performance of the machining process.
- Chip Removal: Some cutting fluids help in flushing away metal chips from the cutting zone, thus preventing machining inaccuracies and prolonging the sump life of the coolant.
- Corrosion Resistance: The right formulation can protect machine components and workpieces against rust and corrosion, thereby ensuring high-quality finishes on metal parts.
Benefits of Using Metal Cutting Coolant
Advantages of Incorporating Metal Cutting Coolants in Processes
Incorporating metal cutting coolants into your processes can significantly enhance the efficiency and longevity of your tools and machines. Here are some benefits to consider:- Improved Tool Life: Metal cutting fluids, such as oils and synthetic coolants, play a critical role in reducing friction and heat during operations. By doing so, they help extend the life of cutting tools, which leads to cost savings in the long run.
- Enhanced Cutting Performance: A high-quality cutting fluid can improve the precision and surface finish of the machined parts. Soluble and semi-synthetic fluids, in particular, are known for their ability to provide optimal cutting conditions, even during heavy-duty tasks like grinding and sawing.
- Reduced Wear and Tear: Implementing effective coolant systems helps lower wear and tear on machines. This translates to less frequent maintenance and ultimately, longer sump life. Water-soluble and moderate-to-heavy duty cutting oils are recommended for operations involving cast iron and similar metals.
- Efficient Lubrication: Metalworking fluids act as lubricants that decrease the coefficient of friction between the tool and the material being cut. Whether you are using low-foaming synthetic coolants or traditional cutting oils, the reduction in friction can lead to smoother operations.
- Productivity Boost: By enhancing tool performance and decreasing downtime due to machine wear, coolants boost overall productivity. This is especially true in high-volume operations where efficiency is key.
Types of Metal Cutting Coolants
Diverse Options in Metal Cutting Fluids
When considering enhancing efficiency with metal cutting coolant, it's crucial to understand the variety of fluids available. The right choice greatly influences not just the process but also tool life and overall machine efficiency. Let’s delve into the types:- Soluble Oils: These are water-soluble and serve as an excellent cooling agent. They offer moderate to heavy-duty cooling, making them a preferred choice for various metal cutting tasks. These oils are particularly effective in cutting and grinding operations, ensuring the longevity of both tool and machine life.
- Semi-synthetic Coolants: These fluids blend the benefits of synthetic and soluble oils, maintaining a balance between cooling and lubrication. They typically have a lower foaming characteristic, ideal for cutting oil in sawing and grinding, where minimizing residue is a must.
- Synthetic Coolants: Without any oil content, these are purely chemical coolant products designed for advanced performance in cutting operations. They often deliver high efficiency in processes involving cast iron and other challenging materials.
- Cutting Oils: Known for their lubricating properties, cutting oils are mainly useful in situations where tool lubrication is critical. They extend the life coolant significantly, particularly in sawing and member joined applications.
- Water-based Coolants: Water soluble, these coolants are straightforward to manage and recycle when compared to oil-based options. They are sustainable alternatives, fitting well into strategies prioritizing environmental considerations.
Choosing the Right Coolant for Your Needs
Selecting the Best Coolant for Optimal Performance
Choosing the right metal cutting fluid is crucial for boosting the efficiency and longevity of tools and machines. There are several factors and options to consider, allowing for informed decision-making.- Material Compatibility: Analyze the material being processed, whether it's cast iron or another metal, as different cutting fluids suit different materials. For instance, heavy-duty operations may benefit from high-performance soluble oils, while lighter tasks might be more effective with water-soluble coolants.
- Coolant Types:
- Cutting Oils: These are pure oils or based on mineral and synthetic oils, suited for extreme pressure applications, like sawing and grinding tasks.
- Water Soluble Coolants: With a composition that allows mixing with water, these suit operations requiring constant lubrication and cooling.
- Semi Synthetic Fluids: These offer a balance between the benefits of synthetic and nature-derived oils, fitting moderate heavy duty and diverse cutting conditions.
- Synthetic Coolants: Containing no oils and usually clear, these avoid residue build-up and are ideal for grinding applications.
- Operation Type: Consider the heat and pressure levels involved in your operations. High-temperature conditions might require coolants specifically designed to dissipate heat efficiently.
- Tool Life Extension: Opting correct fluids not only increases sump life but also extends the life of the tool itself. It's essential to match the tool's requirements with the most suitable product.
- Environmental and Safety Concerns: Choose low foaming, environmentally friendly options to ensure both safety and sustainability in the workplace. While selecting, remember the regulatory implications of the chosen metal cutting fluids and their impact on the environment.
Implementing Coolant Systems in the Workplace
Integrating Coolant Systems Efficiently
Implementing coolant systems in your metal cutting operations can significantly enhance tool life and improve the efficiency of your processes. To integrate these systems effectively, it’s crucial to consider the compatibility with your existing machines and the specific requirements of your production environment.
A well-organized approach will ensure that your cutting and grinding activities are not only smooth but also optimized for both performance and sustainability. Consider these steps when implementing a coolant system:
- Evaluate Your Equipment: Assess the machines used in your metalworking processes. Different tools might require unique types of cutting fluids, such as soluble oils or semi-synthetic options, to ensure peak performance and durability.
- Customize for Your Needs: Not all operations demand heavy duty or low foaming solutions. Analyze the specific needs of each task, whether it's sawing, grinding, or high precision metal cutting, to select the right product that matches your operational conditions and environmental considerations.
- Implement a Centralized System: Consider a centralized distribution system for your cutting fluid or synthetic coolant. This will streamline the process of delivering the right amount of fluid to each workstation, conserving resources and extending sump life.
- Monitor and Adjust Flow Rates: Maintaining consistent fluid flow is crucial to cooling and lubrication processes. Modern machines often allow for precision control of these parameters, providing you with the ability to fine-tune the system as needed.
- Regular Maintenance and Upkeep: Regular checks and maintenance are essential for sustaining the effectiveness of your coolant systems. Over time, coolant can degrade, impacting cooling efficiency and the life of the machines. Implementing a schedule for maintenance can help prevent such issues.
These practices will empower your team to enhance efficiency and extend the life coolant across varied metalworking activities, ultimately contributing to improved productivity and reduced operational costs.
Safety and Environmental Considerations
Ensuring Safe and Environmentally-Conscious Practices
Implementing metal cutting coolant systems in the workplace demands careful consideration of both safety and environmental impacts. The choice of cutting fluids—be it water, oil, or synthetic coolant—not only influences tool life and machine performance but also the overall safety for operators and adherence to environmental regulations. To maintain a safe working environment, ensure that proper ventilation systems are in place to minimize exposure to airborne mists generated during processes like sawing and grinding. Research indicates that prolonged exposure to certain cutting oils and fluids can pose health risks, making it essential to provide adequate personal protective equipment (PPE) for workers. Consider the following safety precautions:- Regular Maintenance: Regularly inspect and maintain coolant systems to prevent leaks or spills. Proper maintenance prolongs the life of your cutting fluids, ensuring consistent performance without unnecessary environmental waste.
- Training: Provide thorough training for all personnel on the safe handling and disposal of metal cutting fluids. This includes understanding the use of soluble oils, semi-synthetic, and synthetic coolants, which vary in their handling requirements.
- Spill Kits: Equip your facility with spill kits to address coolant spills promptly, preventing them from becoming environmental hazards.